2489Views 9Comments
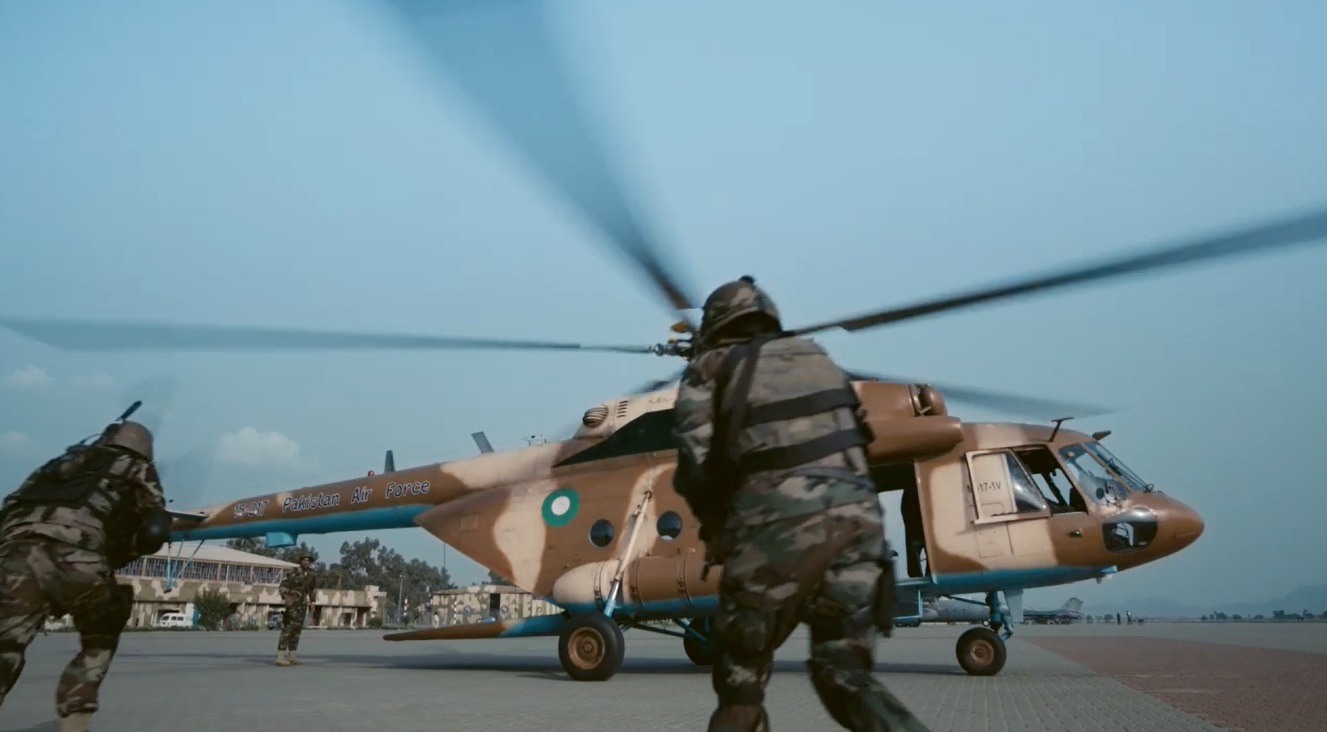
This Week in Review: What would it take for Pakistan to produce helicopters? (Discussion)
Every weekend, Quwa will close the week’s news with a review and analysis with the aim to tie together several topics into broader themes. It is an opportunity to reflect upon and discuss issues in a way where key trends are identified and individual news topics are connected into a “bigger picture.”
This Week in Review: What would it take for Pakistan to produce helicopters? (Discussion)
Foreword: This is not a news story, but a purely analytical piece for the purpose of discussion. There are no officially stated plans in any of Pakistan’s policy circles to engage in domestic helicopter production.
Recently, the Government of Algeria and Leonardo, an Italian defence giant, signed a memorandum of understanding (MoU) to raise a helicopter production facility in Algeria’s Sétif province.
The Ain Arnat facility will offer maintenance, repair, and overhaul (MRO) as well as assembly services to support current and future Algerian helicopter purchases from Leonardo. The specific helicopter types to be dealt with at Ain Arnat have not been disclosed, but according to IHS Jane’s and Defence Web, one could reasonably expect to see the facility manage light and medium-lift helicopters.
In time, Algeria could work towards enhancing Ain Arnat’s capacity, especially genuine manufacturing, which could enable Algeria to become a source of spare parts which Leonardo could use to help sustain its global supply chain.
In response to this news, and potentially in light of the recent launch ceremony of the Pakistan Navy Fleet Tanker, which was produced at Karachi Shipyard & Engineering Works (KSEW) with support from STM Turkey (and championed as an example of domestic production), a number of Quwa readers have raised the question of whether helicopters could be produced in Pakistan. The answer to this question will depend on how one defines “produce.”
Native manufacturing of complex solutions such as aircraft is neither a simple or low-cost avenue. To indigenously produce the airframe in its entirety requires substantial investment in a number of complex and high-value areas. These areas include advanced metallurgy and composite development, precision tooling, and assembly. This is not an exhaustive list, nor does it account for the arduous process of actually designing and developing an airframe from scratch, but genuine manufacturing is a capital intensive task, even for readymade solutions acquired off-the-shelf.
Often times, the task of genuine manufacturing is confused with assembling, the latter is a less intensive task in that it simply involves the assembling of pre-manufactured components. It is also less costly and much easier to implement. Algeria’s deal with Leonardo is not one of genuine manufacturing (at least at this time), but assembly (as well as MRO and training). Yes, the Ain Arnat facility could develop and expand into the area of manufacturing eventually, but this would – at best – be a long-term factor. Moreover, it would require substantial investment, especially if pursued with complete airframe manufacturing (much less turboshaft engine and avionics production) in mind. A more likely route would be parts manufacturing – i.e. a scenario where Algeria produces certain components indigenously, and in turn, supplies them to Leonardo (which can then sell them to third party helicopter users).
In Pakistan’s case, the vast bulk of domestic production is essentially assembly, especially in complex areas such as warship building. Even the Pakistan Navy Fleet Tanker, which had launched for sea trials last week, was produced with manufactured kits supplied from STM Turkey (STM). On the other hand, the Pakistan Aeronautical Complex (PAC) JF-17 is an attempt at building genuine manufacturing capacities in Pakistan, but 42% of the airframe is still imported from China. Yet, the Thunder required a significant investment, and the military’s willingness to back it in this form stemmed from the reality that an alternative avenue for a flexible backbone multi-role fighter was simply not available.
Herein lie several important points. First, the process of building a genuine manufacturing base for just an airframe – much less the engine – is a very expensive proposition, even for wealthy countries. Second, Pakistan’s own ability to manufacture complex solutions is still in its infancy. Third, the motivation to enter manufacturing works has to stem from absolute necessity. In terms of the third factor, if an affordable and sufficiently capable alternative exists, even as a straightforward import, Pakistan will almost certainly take up that available platform (and abandon the idea of domestic development or manufacturing). Ultimately, the Pakistani military is a cost-sensitive entity.
One might propose the idea of standardizing the operational needs of armed forces and civilian users within the country as a means to create scale, which in turn could justify the costs of bringing in-house helicopter manufacturing. In theory, it is an excellent idea, but the practical implementation may not fit neatly. Each of Pakistan’s service arms has unique operational needs.
For example, the Pakistan Navy requires helicopters that are suited to the maritime warfare environment, i.e. it needs a platform that is resistant to salt-erosion but is also capable of launching an anti-submarine warfare (ASW) torpedo or anti-ship missile (AShM). This platform would also need a capable electronics warfare (EW) and electronics countermeasures (ECM) suite so that it has a chance at surviving in a combat environment. These are very specific requirements, and having to incorporate them into a helicopter design may result in other service arms, such as the Pakistan Army, incurring a ‘cost punishment.’
The Pakistan Army will probably not desire such a complex machine; it simply needs a utility helicopter that it can use to ferry troops and supplies behind enemy lines. Yet, if the helicopter is designed to do much more, then the costs associated with those features will have to be distributed among users who have no need for those features. In other words, the Army, Air Force, law enforcement agencies, and civil services will be stuck paying for a design that is capable of effective ASW. And this is simply the cost of development, never mind the costs associated with actually producing each helicopter (which will include additional costs, such as the cost of building the manufacturing line for that helicopter). While Pakistan’s financial problems are not new, the costs being discussed would impact much wealthier countries.
The case made in this article is in regards to manufacturing and complete standardization, especially under Pakistan’s current political and climate. However, this is not to say that certain steps cannot be taken towards generating a helicopter industry in Pakistan. Platform rationalization (within the Army), domestic MRO, spare parts manufacturing via commercial offsets, and over the long-term, joint-ventures in areas that correspond with actual wide-scale requirements, could be pursued. These will be discussed later in a separate article.
9 Comments
by bill
The first step in starting production is assembling, Pak has been able to do so in terms of JF17 and Ships/subs.
Now at least PAF has taken steps for creation of excellence hub based on synergy of resources i.e from establishment of educational/research institutes to produce required labour force and preparation of whole infrastructure. As China has been able to produce fighter jet engine, Pak can at least get license based production rights for engine from China as in case of Russia this possibility is unlikely.
One may consider that so far Paf in field of designing have enough enough experts now they require infrastructure/labour force for production. Certainly PAF shall have to work extensively in fields of alloys and stealth to enter in field of production, which may take a decade but shall be fruitful in future though looks costly at present.
Now as limited exports of JF17 are starting and one should expect more exports after introduction of more capable block 3 especially to Arab countries and also to some African once. The costs shall be offset by exports. I hope same strategy is in minds of PAF planners, same strategy should be adopted in case of PN. But there we have huge problem as our steel mill is so far incapable to produce required standard steel.
by Navid Butt
Keeping All those financial and technological constraints in mind,my suggestion would be ,we go for the re-engineering /refurbishment of Bell’s Uh1and Ah1 family with either new or overhauld Lycoming T53 Engine (with spare parts being built in country )and the replacement of twin propellers for three.Geopolitical and financial position of USA is such that it will not find difficult to cooperate with Pakistan.Beg,steal,borrow or innovate,get the know how with the help of China,America and Turkey and be prepared for fiscally happier times.There are lots and lots of these one engined military and civilian helicopters,Uh1 can also be used in natural emergencies and Ah1can be converted into UAV (s).
by SP
A few things come to mind. Any product manufactured in Pakistan will need to be produced in sufficient quantity to be a viable proposition. Pakistan has no option but to expand its manufacturing base in order to save foreign exchange when competiting against a much larger rival and needs to spend more to maintain detterence. With the passage of time we need to be able to produce all components of any product and not just assemble the product. The products that Pakistan produces need to constantly evolve and improve with time and not be an example of Mehran Suzuki which eventually becomes producing outdated junk at inflated prices. I also read somewhere that 30% of the budget if the military is “wasted” so there is much room to improve efficiency.
by Nawaf
First of all, all the military divisions along with government and law enforcement agencies should provide their list of requirements and specifications that they require for purchasing a helicopter to a committee setup for buying helicopters. This will include no. of units for each service group, troop capacity, cargo, range, speed, flight ceiling, EW suites, ASW suite, etc. which each service department requires. Then, after evaluating the requirements the committe could conclude which type of helicopter should they buy which will suit all the service branches with modications and updates. If the combine demand of helicopters ranges from 100-150 units with different avionic, EW, Ground and ASW suites they those systems could be added for different service branches but keeping the same basic airframe, enigines and design. This will keep the costs lower and give economies of scale with same level of engine and spare parts for all the helicopters in the future. This is the ideal situation where the helicopters could be domestically produced and be beneficial in the long term.
by middleway1
This is not directly related to this post, but I would like Bilal to write an article on why we should or should not pursue sharing defense technology with Iran now that sanctions have been lifted. I was struck by this news item today, “Rouhani also unveiled the first Iranian-made turbo-jet engine on Sunday, saying it was capable of flight at 50,000 feet. “The Islamic republic is one of eight countries in the world who have mastered the technology to build these engines,” the president said.” They have also developed an indigenous missile defense system, and have advanced indigenous drone technology as well. Do we have anything to offer them in return?
by Hashim Rasheed
Even if there is no step to produce helicopters locally, it still makes sense to carry out research and try to develop technologies that may work towards building capacity for developing helicopters. In the long run, this will be the most viable option as Pakistan’s fiscal problems will not go away any time soon, and their requirements for refurbishing and re-arming the forces will keep increasing, It should be kept in mind that Pakistan’s defense forces are still reliant on quite old technology, and sooner or later, there will be a time to replace the currently used platforms with newer ones.
Developing expertise and technical knowledge for airborne weapons and platforms is the only option Pakistan’s forces can stand the test of time, with increasing hostility on both the Eastern and Western front. Developing a platform for CAS operations with minimum but effective payload capacity could be a first step towards achieving the goals of the armed forces. Just like the JF-17, it could serve as the first step towards development and integration of more sophisticated suites and weapons.
by Dano Ali
Everything depends on the size of investments, which can be pumped and the size of which can be purchased aircraft bombed
by Sheharyar Hassan Khan
The idea is not bad at all – but even the idea of sharing technologies with Iran will come up to face the political pressure from US and Saudi Arabia. The gas pipeline project is an example of this problem which after years of work is still not completed.
by middleway1
The pressure against the pipeline was because of the sanctions on Iran at the time. With the sanctions removed, Pakistan has more freedom to engage in trade and technology transfer with Iran, except, of course, nuclear technology. If Pakistan proceeds in this direction, the Western powers and India will still not like it, just like they don’t like it’s relationship with China. Pakistan needs to balance it’s relationship between Saudi Arabia and Iran. Saudi Arabia is a money donor at best, while Iran is a far more developed and technologically advanced country in comparison. Iran even has a more highly developed chemical and biological industrial base than Pakistan. Their research output is higher quality and one of the highest in the Muslim world, I believe second only to Turkey. Pakistani research is measly and low quality by comparison. There is a lot we can learn from Iran.